The rapid prototype plastic vacuum molding process is widely used in the manufacturing industry. Due to its low cost, high efficiency, and high precision, this process has become a powerful assistant for many enterprises in innovative research and development. In the early stages of product design, when traditional methods appear expensive or impractical, vacuum replication technology can produce parts that are highly consistent with the prototype at an extremely low cost in a short period of time, providing strong support for rapid validation and iteration of product design.
Application area:
The plastic vacuum molding process is widely used in multiple industries, especially for producing prototype parts in NPD stage, including automobiles, consumer electronics, healthcare, toys, handicrafts, and character reproduction. The specific application areas are as follows:
Automotive components prototyping industry: used to produce door interior panels, door interior panel inserts, armrests, roof panels, and other components for various sedans.
Consumer electronics components prototyping industry: used for making various small batch plastic components.
Medical equipment components prototyping industry: Used to make components of medical equipment with complex structures.
Toys and crafts prototype fabrication industry: used for making high-precision replicas of toys and crafts.
Operation steps:
The specific operational steps of rapid plastic prototype vacuum molding processes include:
Step #1, preparation of master mold: Use SLA laser rapid prototyping or CNC machining to create a prototype, then use silicone inverted mold to make the mold, leaving the water outlet and exhaust hole.
Step #2, making silicone molds: Pour liquid silicone into the mold, eliminate bubbles, and cure.
Step #3, casting molding: Inject the prepared raw materials into the mold through a fixed feeding port, fill it up, and place it in an oven to accelerate material solidification. After the material solidifies, remove the mold and open it to obtain the desired product.
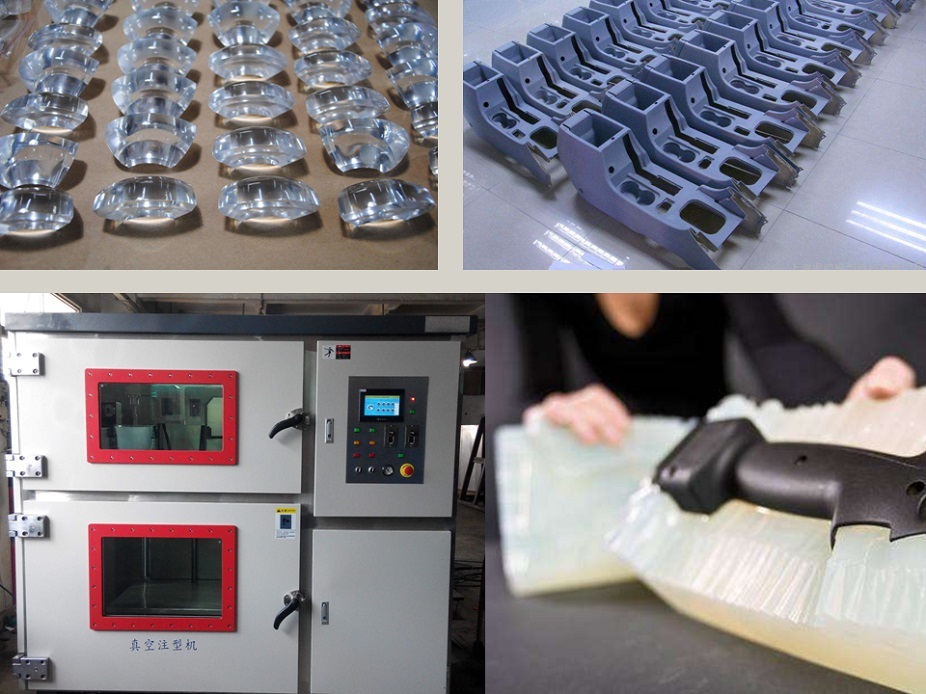